傳統產品製造業中所使用的資訊應用系統通常只有 ERP,如果對產品製造有產線即時資訊收集、生產流程及品質控管、產品履歷追蹤等需求,則會另外導入 MES 系統。由於 ERP 系統架構偏規劃面(Planning),而 MES 重執行面(Execution),因屬性不同一般都是獨立運作,頂多做些簡單的批次資料交換。但由於企業經營與生產管理的觀念進化,加上資訊應用軟體整合技術的進步,企業內部的資訊系統都要能無縫整合,製造產業對於 ERP 及 MES 兩大系統更是殷切期盼能完全整合。
我們先從企業資源的角度來看,ERP 管理企業的四大資源:4M(資金 Money、製品原料 Material、人員 Man、生產機器 Machine);而 MES 涵蓋其中的三項:製品 + 在製品 + 原料(Material)、生產機器產能及維護(Machine)、人員投入與配置(Man)(表一)。由此可見,這兩個系統涵蓋的管理資源範圍幾乎相同,而產品生命週期(圖一)各階段資訊流的串聯也是兩相互補接軌。
表一、ERP 與 MES 所對應的企業資源管理項目
企業資源 | ERP | MES |
---|---|---|
資金(Money) | v | |
製品原料(Material) | v | v |
生產機器(Machine) | v | v |
人員(Man) | v | v |
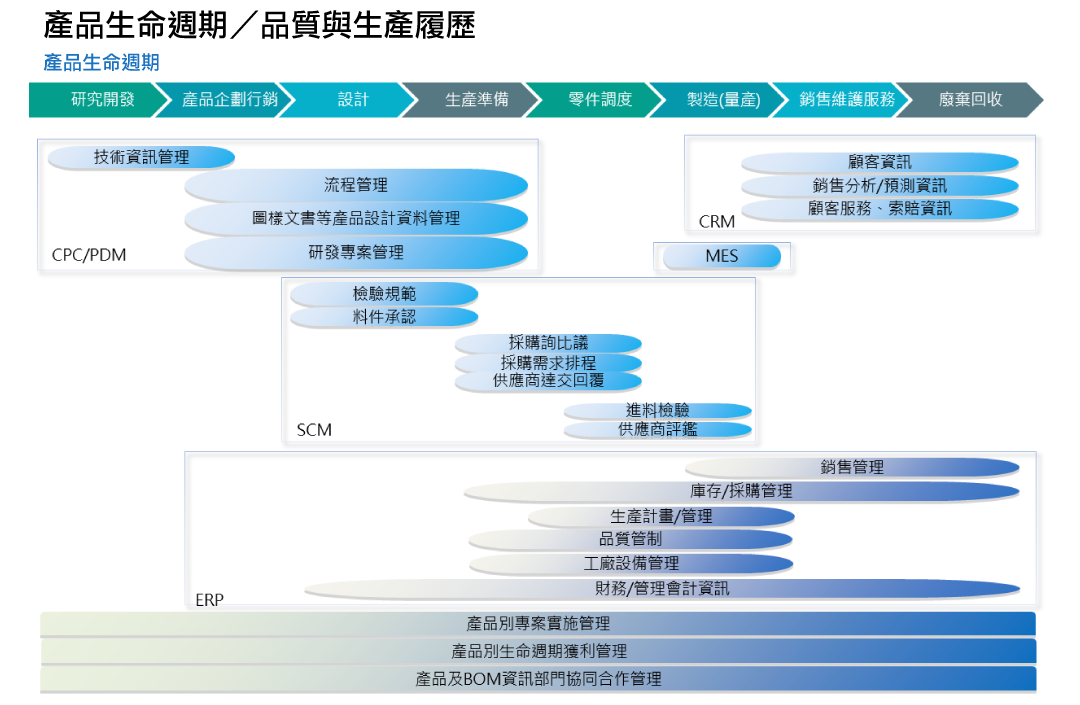
現在的套裝資訊軟體系統皆可透過參數化設定來對應需求,一般企業的財務會計、銷售採購、成本計算、內稽內控…等管理需求,都可以透過 ERP 的參數化設定符合企業內部作業流程。而生產製造管理也有一定的相似性可透過 MES 的參數化設定來對應,但是因為產業生產品及製造現場配置的不同、機台設備自動化程度與作業人員專業技術層次的落差,必須因時、因地、因人而有更大的彈性配合,所以在初期規劃階段需要專業顧問深入了解提出符合成本效益的規劃。
以業務形態提供不同的解決方案
- 案例一:企業為來料受託加工的生產型態。因為原料都是客戶提供,企業只需提供場地及人力進行加工,所以企業管理的重點在於數千名作業人員的晉用調度、出缺勤、加班、按件計酬、用餐住宿…等記錄。
- 案例二:企業為專業 OEM(Original Equipment Manufacturer;代工生產)廠商。因應國際大廠客戶要求全製程產品需要生產履歷資料收集、跨國廠區不同生產製程在製品移轉、千點以上工作站點全人工或半自動製程資料收集。
- 案例三:企業為全自動生產線,提供軍用、車用等高階及嚴格安規要求的產品。需要生產機台連線自動資料收集、量測儀器連線即時檢驗控管、SCADA(Supervisory Control And Data Acquisition;數據採集與監控系統)平台動態圖表展示、即時異常警示通知、行動設備即時連線作業、自製或委外在製品流向追蹤、線邊倉庫即時用料管理、製造成本動因收集回饋、售後客服資訊串接…等。
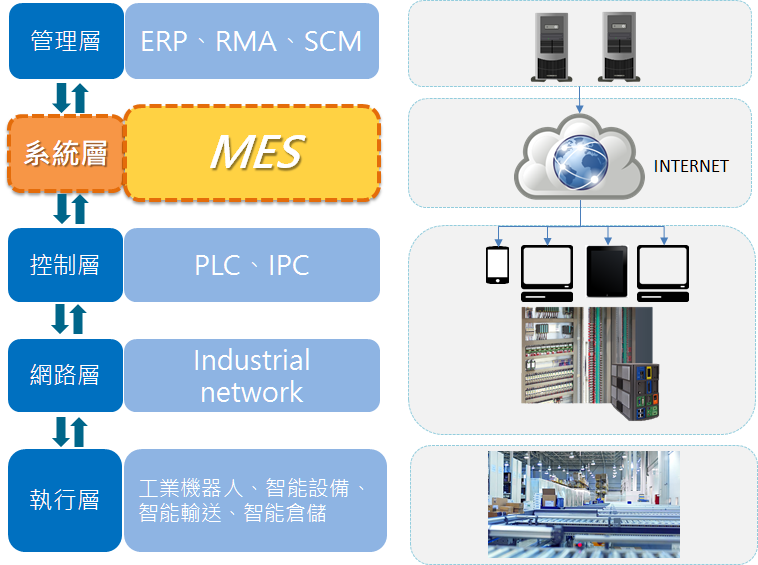
透過以上不同型態企業的成功案例,能了解 ERP 可根據客戶不同成長階段或是產業特性,透過專業規劃替客戶提供適用的應用資訊軟體產品組合,並由專業產業顧問進行最適切的作業流程優化建議及資訊系統導入,建構具效益、有生產力的企業資訊系統!